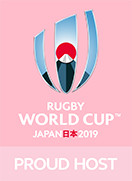
Iga Kumihimo
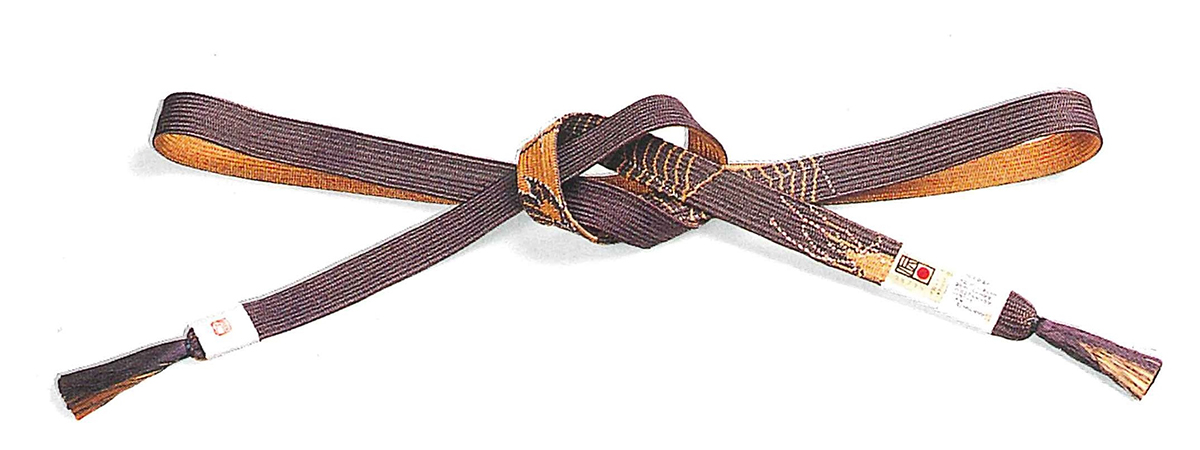
The traditional technique for making kumihimo is based on that for sageo cords, used by samurai as decoration on the scabbards of their swords.
In the Meiji era, people began to use kumihimo to secure obi (sashes worn with kimono) and haori (a short Coat for formal kimono).
There are currently about 3,000 braiders in Ueno, the largest kumihimo producing area in Japan.
Manufacturing of kumihimo starts with making silk yarn; weighing and sorting the raw silk, dyeing, and then twisting.
Then comes the braiding process.
This is performed with various braiding stands; there are the takadai (high stand), marudai (round stand) and kakudai (square stand).
The stands can accommodate different numbers of bobbins, each combination resulting in a braid of different structure and design.
As many as 60 different exquisitely detailed patterns can be made with a takadai.
The artisan hits the braid with a spatula after each twist with the same angle and force.
It is work requiring a great deal of concentration and persistence.
In the Meiji era, people began to use kumihimo to secure obi (sashes worn with kimono) and haori (a short Coat for formal kimono).
There are currently about 3,000 braiders in Ueno, the largest kumihimo producing area in Japan.
Manufacturing of kumihimo starts with making silk yarn; weighing and sorting the raw silk, dyeing, and then twisting.
Then comes the braiding process.
This is performed with various braiding stands; there are the takadai (high stand), marudai (round stand) and kakudai (square stand).
The stands can accommodate different numbers of bobbins, each combination resulting in a braid of different structure and design.
As many as 60 different exquisitely detailed patterns can be made with a takadai.
The artisan hits the braid with a spatula after each twist with the same angle and force.
It is work requiring a great deal of concentration and persistence.
TM © Rugby World Cup Limited 2015. All rights reserved.